What is inventory planning ?
Inventory planning is an important process for businesses of all sizes. It is the process of determining what to order when to order, and how much to order. This process is important because it can affect business profitability. If there are not enough products to meet customer demand, the company will experience a shortage. This will cause customers to buy from competitors instead. If there are too many products, then the inventory will be wasted and the company will not reach its full potential. The process of creating an inventory plan to determine the quantities of inventory to order, produce, or store. Inventory planning is the process of creating an inventory plan to determine the quantities of inventory to order, produce, or store. It includes balancing inventory across the distribution channels, the products, and the timing of the purchases. It also includes inventory forecasting, inventory control, and tactical inventory management.
What Is Inventory Planning, How Do You Do It, And How Can You Benefit?
What is Inventory Planning?
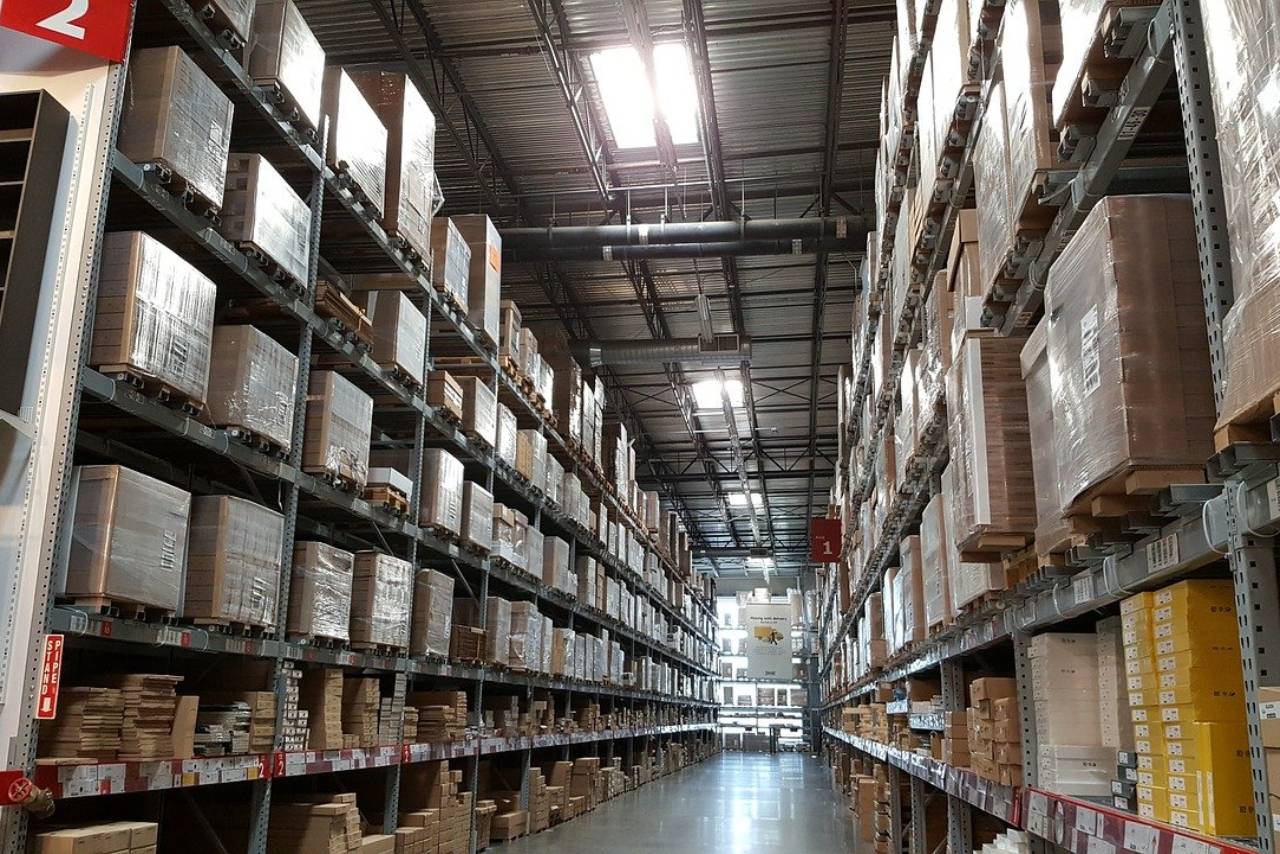
Inventory planning is a part of the larger inventory management. Organizations adopt this process to determine the exact quantity and the timing as per their production and sales capacity. This is an integral part of an organization's supply chain management strategy along with warehouse management, accounting, order management, and customer service.
Inventory is one of the most important business assets. Businesses need to operate continuously. However, holding too much inventory damages the healthy cash flow of the business. It restricts the growth of the business as a major amount is tied up in excess inventory and cannot be invested in other important areas of the business. In the restaurant industry, excess inventory like food and beverage leads to wastage and subsequent loss.
The process of inventory planning involves demand forecasting for deciding the order quantity and when to order. Successful inventory forecasting helps businesses to meet demand and simultaneously reduce holding costs. With the right inventory available at the right time like time inventory, businesses can reduce storage costs. Inventory optimization in a business ensures the presence of the right stock levels to meet customer demand.
Businesses ensure a smooth cash flow by planning inventory and generating profits along with building efficient supply chains. Various case studies show that implementing inventory management software in the organization, reduces the lead time, streamlines the process of inventory planning inventory control, and simplifies the entire chain management.
Inventory is one of the most important business assets. Businesses need to operate continuously. However, holding too much inventory damages the healthy cash flow of the business. It restricts the growth of the business as a major amount is tied up in excess inventory and cannot be invested in other important areas of the business. In the restaurant industry, excess inventory like food and beverage leads to wastage and subsequent loss.
The process of inventory planning involves demand forecasting for deciding the order quantity and when to order. Successful inventory forecasting helps businesses to meet demand and simultaneously reduce holding costs. With the right inventory available at the right time like time inventory, businesses can reduce storage costs. Inventory optimization in a business ensures the presence of the right stock levels to meet customer demand.
Businesses ensure a smooth cash flow by planning inventory and generating profits along with building efficient supply chains. Various case studies show that implementing inventory management software in the organization, reduces the lead time, streamlines the process of inventory planning inventory control, and simplifies the entire chain management.
The Importance of Inventory Planning
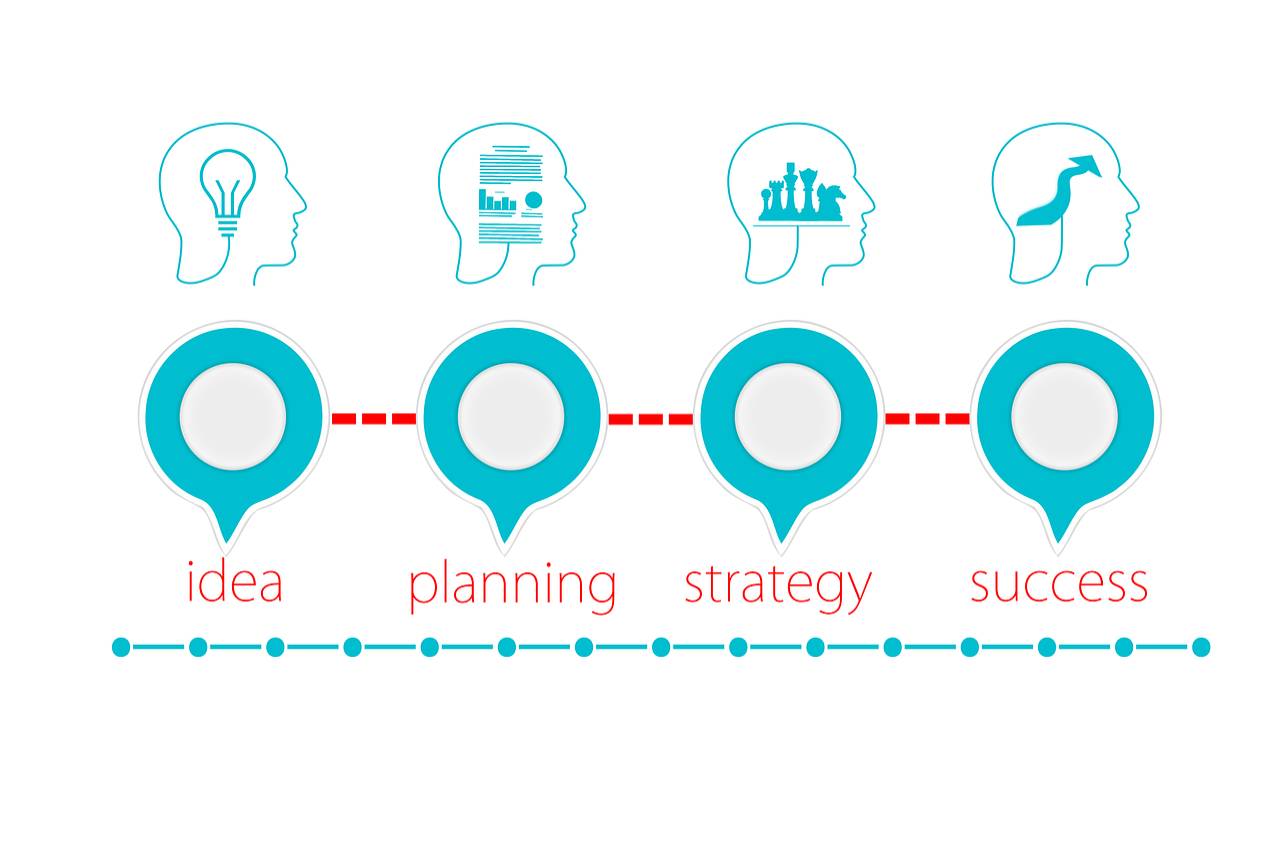
Good inventory planning is important because it helps to maintain a balance between overstock and stockout. While over-storing inventory can create a budget deficit, low stock levels can compromise customer satisfaction. In addition to inventory cost, carrying cost also adds up. A marginal loss percentage is common in managing inventory however a larger amount can hurt the profit levels. This is why inventory planning is essential to manage inventory. It helps businesses to reduce the loss through inventory mismanagement. Inventory planning is necessary to improve customer satisfaction rates and prevent overselling thereby maintaining consistent service levels. According to a 2020 survey report from Statista, 1/5th of businesses plan on storing more inventory post-pandemic.
Here are the main reasons for inventory planning-
The best strategy for maintaining effective inventory planning depends on those parts of a business that needs improvement. An assessment of the inventory management process would help determine the weak links in the business operation. Using inventory planning and management software can make the process easier. Methods like demand forecasting formula, economic order quantity, continuous and periodic ordering are helpful while planning inventory.
Here are the main reasons for inventory planning-
- To prevent overselling and creating a bad customer experience.
- To control inventory costs and maintain inventory turnover.
- To ensure smooth cash flow as excess inventory ties up cash and obstructs other processes.
- To meet demand and increase customer satisfaction.
The best strategy for maintaining effective inventory planning depends on those parts of a business that needs improvement. An assessment of the inventory management process would help determine the weak links in the business operation. Using inventory planning and management software can make the process easier. Methods like demand forecasting formula, economic order quantity, continuous and periodic ordering are helpful while planning inventory.
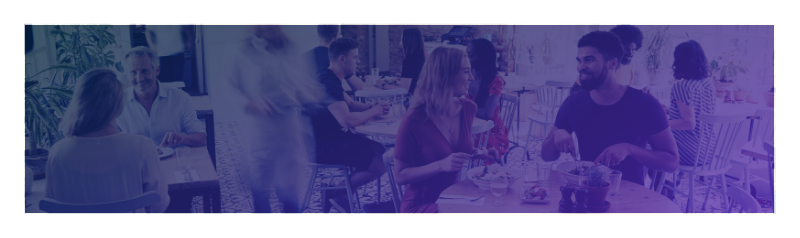
Running low on inventory can be a huge problem for your business.
You could lose sales if you run out of stock, and you could also lose customers if you charge too much for shipping.
How To Do Inventory Planning
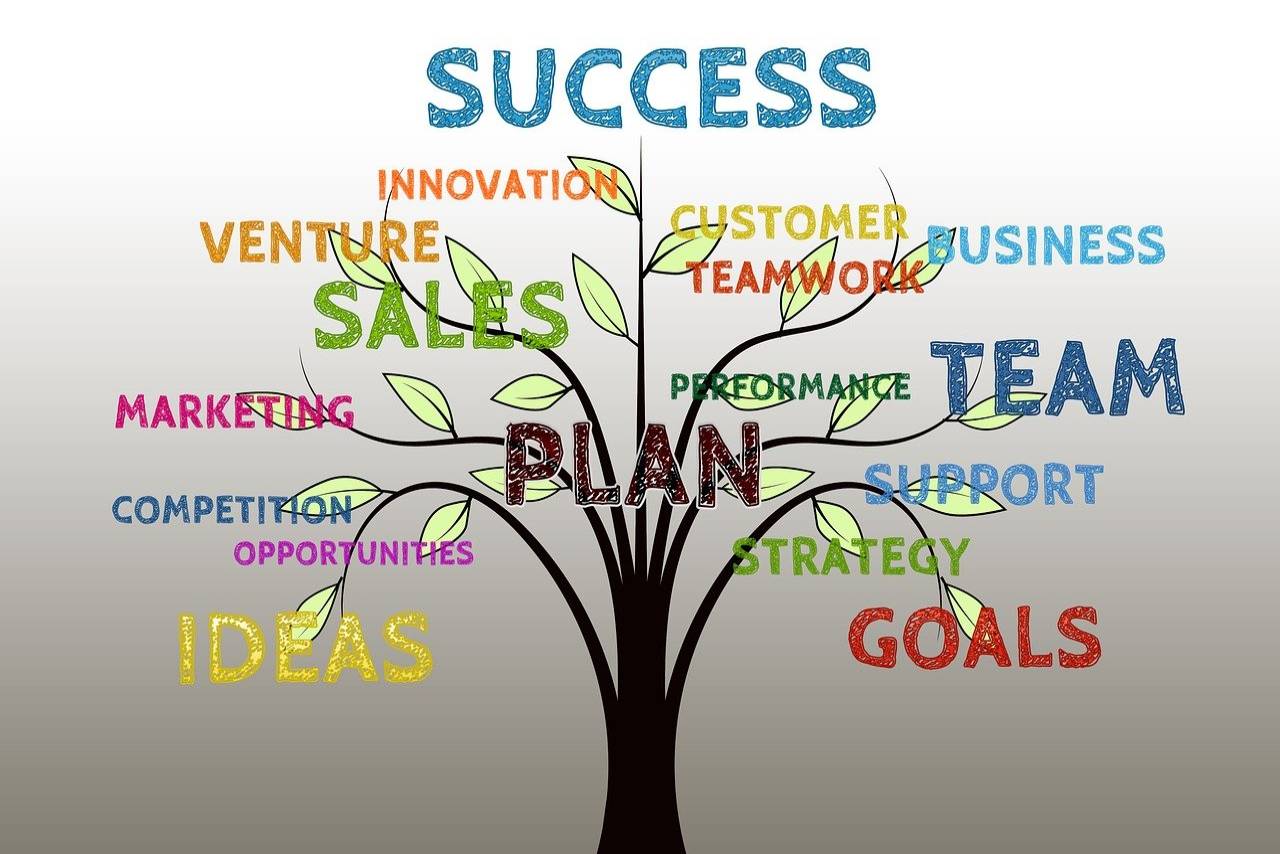
Context, analytics, and planning are necessary for a successful inventory plan. Data from business history, sales order, competitor landscape, present social and political events all are necessary for the inventory planning process.
The inventory planning process involves the following steps-
Inventory planning systems are unique to the type of a business and its needs. Any small business dealing in raw material, partially completed goods, or finished goods must select the inventory planning model that meets all its requirements.
Just in time inventory model- The time inventory model or time jit inventory planning synchronizes the orders of raw materials from suppliers with the production planning schedule. This planning model requires accurate demand forecasting to ensure the availability of sufficient inventory and meet the maximum demand. The time jit method increases efficiency and decreases wastage as businesses use inventory as soon as it arrives.
Deterministic inventory model- Applicable for any small business dealing in raw materials, the deterministic inventory planning model uses a precautionary method to avoid a shortage of inventory items. The economic order quantity is an example of the deterministic inventory model. The economic order model refers to the ideal order quantity that any business should purchase for minimizing its inventory costs. The EOQ model ensures the right amount of inventory is ordered so that there is no excess inventory. The economic order quantity is effective when the demand is steady. However, the order quantity EOQ model is not suitable for seasonal changes in demand. For a successful quantity, EOQinventory planning model businesses have to monitor it constantly.
Work in progress model- This inventory management method is suitable for businesses dealing with partially completed or finished goods and goods in transit. This model prioritizes holding inventory for protecting against demand uncertainties and alleviating the price increase of raw materials or labor.
Perpetual Inventory planning model- This continuous inventory model is preferred by businesses dealing with finished goods. This inventory system tracks the inventory quantities and sends orders to replenish the inventory when the amount reaches the reorder points to maintain safety stock. This inventory planning model requires inventory management software to keep track of current stock levels and avoid any shortage.
The inventory planning process involves the following steps-
- Gathering the necessary business data including competitor's details.
- Understanding the performance of stock-keeping units and using them to set upcoming expectations.
- Setting flexible budget according to product category.
- Check weekly reports to determine performance and forecast demand periodically.
- Use monthly sales forecast to manage consistent inventory
- Analyze the performance at the end of the season and make necessary changes for the next season's inventory planning.
Inventory planning systems are unique to the type of a business and its needs. Any small business dealing in raw material, partially completed goods, or finished goods must select the inventory planning model that meets all its requirements.
Just in time inventory model- The time inventory model or time jit inventory planning synchronizes the orders of raw materials from suppliers with the production planning schedule. This planning model requires accurate demand forecasting to ensure the availability of sufficient inventory and meet the maximum demand. The time jit method increases efficiency and decreases wastage as businesses use inventory as soon as it arrives.
Deterministic inventory model- Applicable for any small business dealing in raw materials, the deterministic inventory planning model uses a precautionary method to avoid a shortage of inventory items. The economic order quantity is an example of the deterministic inventory model. The economic order model refers to the ideal order quantity that any business should purchase for minimizing its inventory costs. The EOQ model ensures the right amount of inventory is ordered so that there is no excess inventory. The economic order quantity is effective when the demand is steady. However, the order quantity EOQ model is not suitable for seasonal changes in demand. For a successful quantity, EOQinventory planning model businesses have to monitor it constantly.
Work in progress model- This inventory management method is suitable for businesses dealing with partially completed or finished goods and goods in transit. This model prioritizes holding inventory for protecting against demand uncertainties and alleviating the price increase of raw materials or labor.
Perpetual Inventory planning model- This continuous inventory model is preferred by businesses dealing with finished goods. This inventory system tracks the inventory quantities and sends orders to replenish the inventory when the amount reaches the reorder points to maintain safety stock. This inventory planning model requires inventory management software to keep track of current stock levels and avoid any shortage.
How Can You Benefit From Inventory Planning?
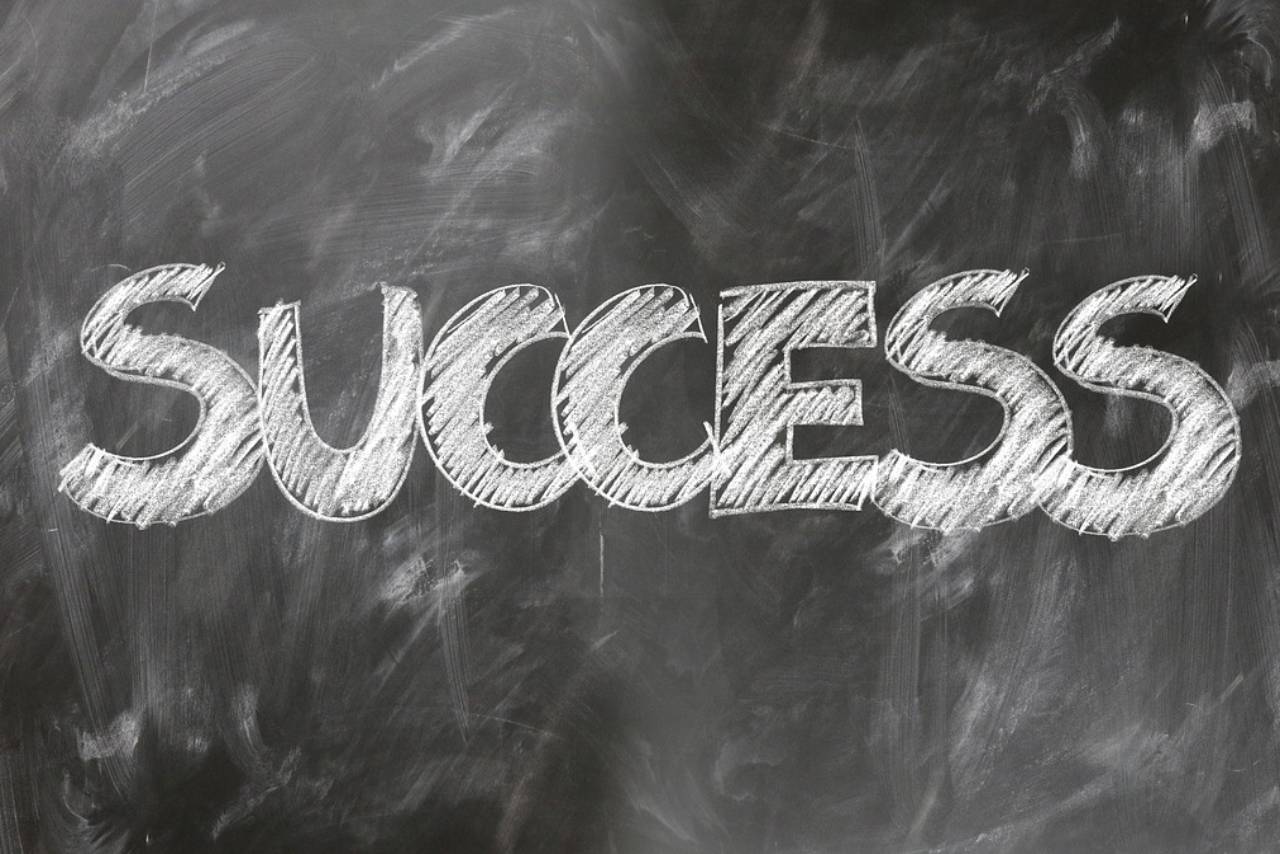
Inventory planning plays an important role in a successful business. It determines the cash flow and related profit margins. It helps in demand forecasting and preparing the business for the upcoming sales. It prevents overstocking or understocking and ensures customer satisfaction with a steady inventory.
For any small business with limited capital, ensuring a steady cash flow is crucial to continue business operations. Internal policy and procedure benefits inventory and control production and sales. By implementing proper strategies, businesses can control their cash flow.
Inventory control can generate higher profits for a business. Invnetory management software benefits inventory planning. With an efficient inventory management system, businesses can maximize production and decrease production costs. The procedures and policies implemented by inventory planning prevent the employees from abusing inventory.
With inventory management software tracking all the items in real time from their origin to the sales, it reduces the chances of theft or misuse. Management Software Best suited for small businesses is the one that offers scalability and customization. It enables businesses to select and use third party inventory management software as per their requirements.
For any small business with limited capital, ensuring a steady cash flow is crucial to continue business operations. Internal policy and procedure benefits inventory and control production and sales. By implementing proper strategies, businesses can control their cash flow.
Inventory control can generate higher profits for a business. Invnetory management software benefits inventory planning. With an efficient inventory management system, businesses can maximize production and decrease production costs. The procedures and policies implemented by inventory planning prevent the employees from abusing inventory.
With inventory management software tracking all the items in real time from their origin to the sales, it reduces the chances of theft or misuse. Management Software Best suited for small businesses is the one that offers scalability and customization. It enables businesses to select and use third party inventory management software as per their requirements.
Considerations for Inventory Planning
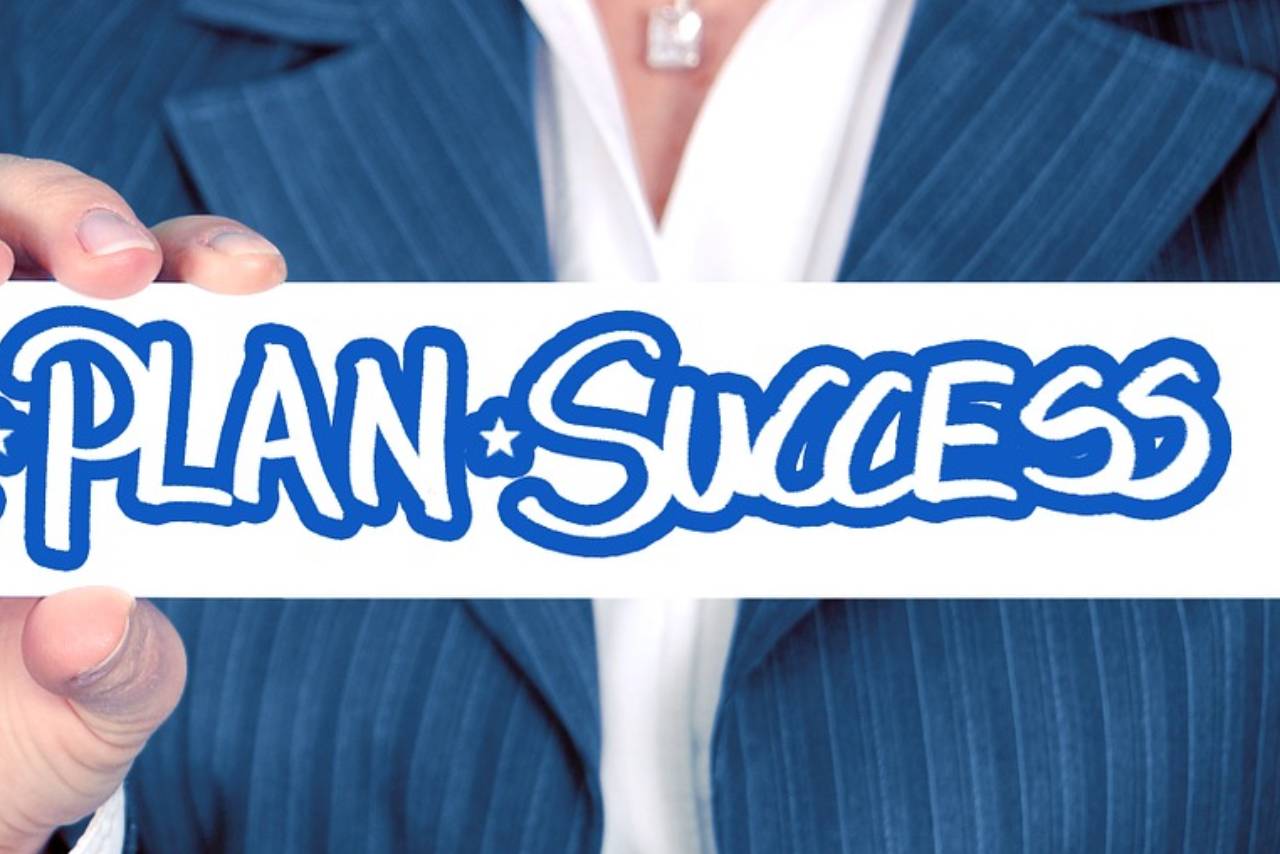
Setting up best practices and procedures is one of the key considerations for inventory planning. The entire process of inventory planning involves human expertise, appropriate strategies, and the right tools like any management software. Before developing an inventory management plan, businesses must go through their past data, seasonality, and other trends to understand the product order quantity. Analyzing past data will reveal any demand spikes. At this point, businesses can use the economic order quantity or EOQ model to determine the right quantity of stock.
While planning inventory company should also consider any internal or external factors that could affect the customer demand. Ad campaigns, promotions, market competition, seasonal demand surges, trends are some factors that can then impact the future demand. Inventory planning should increase the efficiency of business operations. From warehouse management to order processing, inventory planning should help establish a well-organized system. To assess the performance of the inventory management system it is necessary to consider factors like storage capacity, system and forecast accuracy, daily sales, sales inventory, inventory movement, customer satisfaction, inventory turnover, and carrying cost.
While planning inventory company should also consider any internal or external factors that could affect the customer demand. Ad campaigns, promotions, market competition, seasonal demand surges, trends are some factors that can then impact the future demand. Inventory planning should increase the efficiency of business operations. From warehouse management to order processing, inventory planning should help establish a well-organized system. To assess the performance of the inventory management system it is necessary to consider factors like storage capacity, system and forecast accuracy, daily sales, sales inventory, inventory movement, customer satisfaction, inventory turnover, and carrying cost.
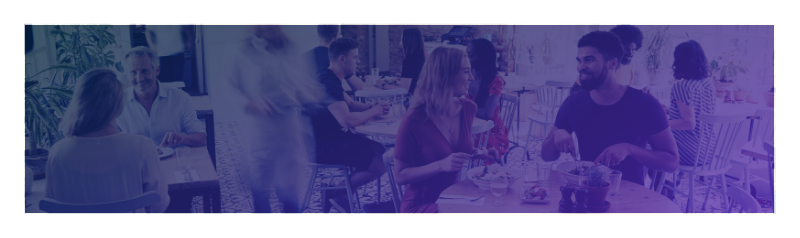
Inventory planning is a crucial part of business, but it's also one that many companies struggle with.
Inventory planning can be difficult to understand and more difficult to implement.
The Purpose of Inventory Planning
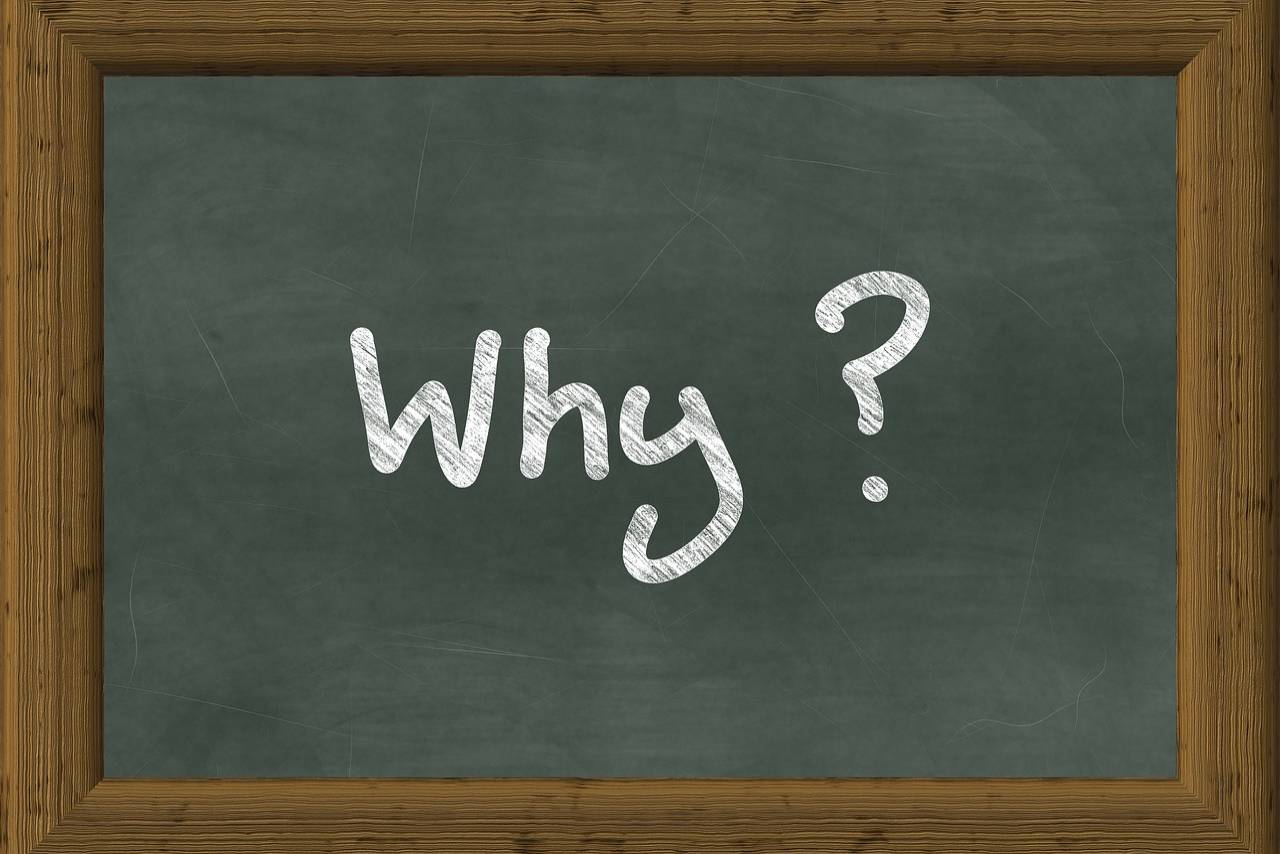
Inventory planning helps businesses to purchase the correct amount of inventory to prevent any wastage. It also helps to make an informed decision about when to restock. An essential part of Supply Chain management, inventory planning influences the cash flow and dictates the profit. Technology can help improve the process of inventory planning. With the right inventory management software businesses can streamline their entire Inventory Management and inventory planning process.
A small business may find it economical to use an Excel sheet or manually enter the inventory details and plan accordingly. However, Inventory Management would become difficult as the business grows. Management software with features like location and sales tracking, barcode scanning, multi-channel management, fulfillment planning, data-driven demand forecasting, reporting, and analytics can help a lot in inventory planning.
Inventory management software reduces manual error and brings efficiency into business operations. Many management software is available for free. Businesses can also opt for a free trial to experience the advanced management system firsthand. These digital systems can store data and use artificial intelligence to help in demand forecasting. Most free versions offer a limited range of features with rights reserved. The strong privacy policy of cloud-based pos inventory management systems keeps user data safe. Small businesses can opt for monthly subscription plans and upgrade later according to business requirements.
A small business may find it economical to use an Excel sheet or manually enter the inventory details and plan accordingly. However, Inventory Management would become difficult as the business grows. Management software with features like location and sales tracking, barcode scanning, multi-channel management, fulfillment planning, data-driven demand forecasting, reporting, and analytics can help a lot in inventory planning.
Inventory management software reduces manual error and brings efficiency into business operations. Many management software is available for free. Businesses can also opt for a free trial to experience the advanced management system firsthand. These digital systems can store data and use artificial intelligence to help in demand forecasting. Most free versions offer a limited range of features with rights reserved. The strong privacy policy of cloud-based pos inventory management systems keeps user data safe. Small businesses can opt for monthly subscription plans and upgrade later according to business requirements.
The Problem with Inventory Planning
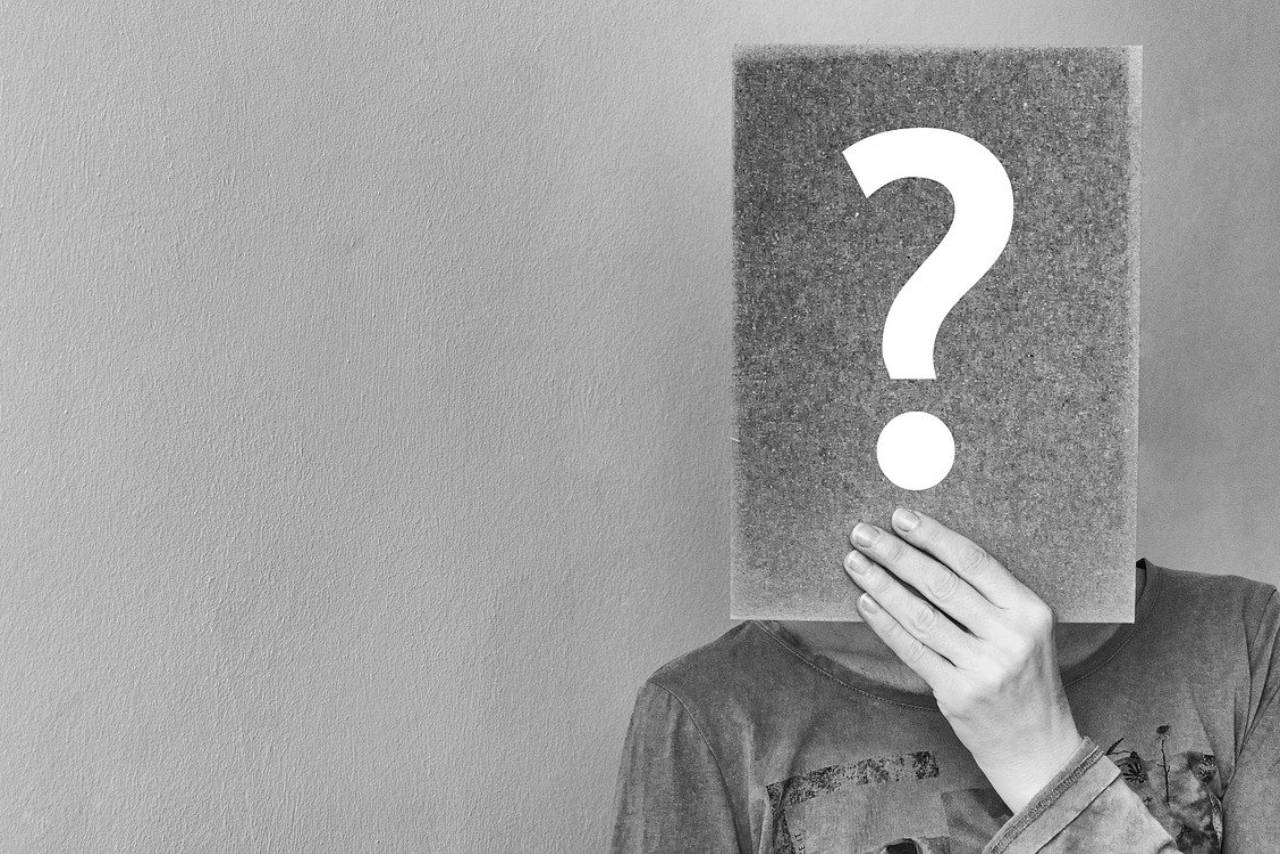
While inventory planning increases efficiency and streamlines the Inventory Management process, it comes with its own set of challenges. Inventory planning is much easier for a small business operating on a single sales channel compared to a business using multiple channels.
Some common problems with inventory planning are as follows-
Too much data- Successful inventory planning requires many data. Sales data, business history, accounting data, suppliers, fulfillment, pos data, and many more are necessary for inventory planning. However, it is time-consuming to bring all these data together and derive the necessary information from them.
Accurate forecasting- Sales or demand forecasting is never full proof. Even with all the data, it is still guesswork. An unpredictable market is another factor that can affect forecasting.
Multiple locations- Manually tracking and allocating inventory across multiple locations is difficult. Storing in the wrong place can generate additional carrying costs and affect customer experience. Using inbuilt inventory management software from pos systems can help in this part.
Planners- Even with all the latest technology businesses would still require a human to enter the details into the system and make informed decisions. An inventory planner must understand the business process before beginning the planning process. This person must also be familiar with the inventory management system to use every available functionality to its fullest.
Some common problems with inventory planning are as follows-
Too much data- Successful inventory planning requires many data. Sales data, business history, accounting data, suppliers, fulfillment, pos data, and many more are necessary for inventory planning. However, it is time-consuming to bring all these data together and derive the necessary information from them.
Accurate forecasting- Sales or demand forecasting is never full proof. Even with all the data, it is still guesswork. An unpredictable market is another factor that can affect forecasting.
Multiple locations- Manually tracking and allocating inventory across multiple locations is difficult. Storing in the wrong place can generate additional carrying costs and affect customer experience. Using inbuilt inventory management software from pos systems can help in this part.
Planners- Even with all the latest technology businesses would still require a human to enter the details into the system and make informed decisions. An inventory planner must understand the business process before beginning the planning process. This person must also be familiar with the inventory management system to use every available functionality to its fullest.
Recommended
Frequently Asked Questions
What are the 4 types of inventory?
Your company's inventory is an important part of your business. It's always a good idea to track your inventory to make sure you don't run out of stock unexpectedly. Inventory is an expense for your company, so it's important to know what type of inventory you have to make sure you don't overspend. There are 4 types of inventory- - raw materials, - work-in-progress, - finished goods and packing material, - MRO supplies.
What are the different methods of inventory planning?
There are many ways to plan inventory in a company. The most common are EOQ or Economic Order Quantity, MRP or Material Requirements Planning, and LIFO or Last In, First Out. EOQ is a method for determining how much inventory to buy when the demand is uncertain. MRP is a method for determining the required inventory levels based on the demand for each item. LIFO is a method for determining the oldest inventory when the demand for an item is uncertain.
What are the objectives of inventory planning?
Inventory planning is a process that is used to reduce the amount of inventory a company carries. Inventory is a resource that a company must either pay for or borrow against. It can be used as a buffer against excess demand or as a source of supply when demand is less than forecasted. Inventory planners use a variety of methods to calculate what is needed, from a high demand forecast to a low demand forecast. Inventory planning is a process that is often done by a department of a company.